MEASUREMENTS, CONTROLLING AND ADJUSTMENTS AT BOILER STRUCTURES IN POWER PLANTS AND COMBINED HEAT & POWER PLANTS

Particular risk is associated with overloading the rods which causes their yielding. Lack of control over the phenomenon of creeping material from which the rods are made may result in serious failures affecting the safety of operator’s work. This can lead to a situation in which the incorrect way of suspending the boiler elements, e.g. a steam super-heater as well as the lack of monitoring of forces in the rods, becomes one of the causes of damage to the suspensions.
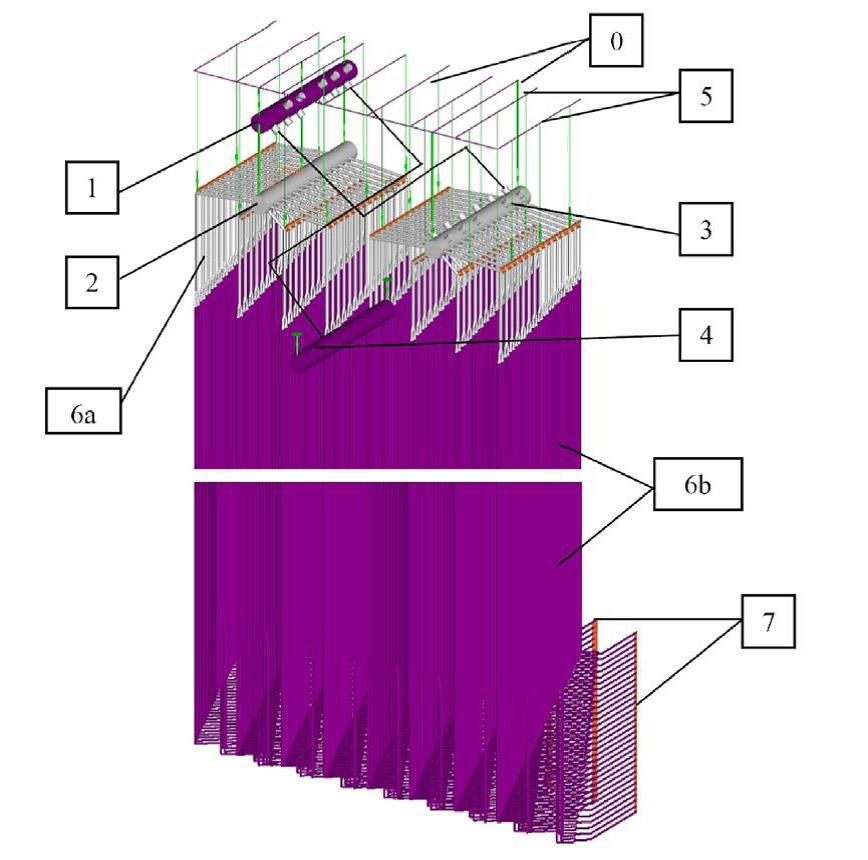
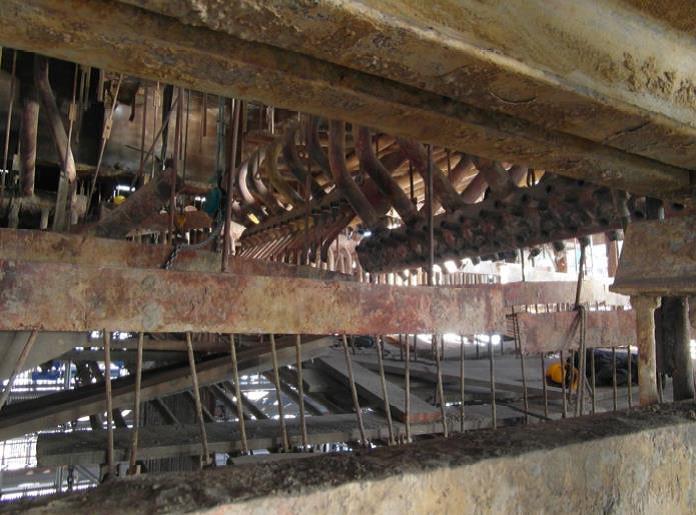
The photo above shows a fragment of a damaged steam super-heater, after breaking the suspension rods. The aspects of safety, lifetime, reliability and repair costs which are related to the operation of boilers and possible failures, encourage boiler designers and users to take a comprehensive approach to the subject of regulation, monitoring and methods of determining forces in suspension rods.
Have a look at the new innovative method of determining forces in
suspension rods of hanging boilers. The main reason of an inaccuracy in the measurement of force in the rods, in the
method currently used on the market, is the difficulty in determining the moment
when the nut is being loosened – the photo below. Even a slight lift of the nut causes
a sudden increase in force in the rod. Measurement errors with the traditional
method are additionally increased due to the difficult environmental conditions
prevailing on the boiler – dust, temperature fluctuations, sometimes limited
visibility or insufficient lighting and difficulties in access to rods. The accuracy of
the measurement also depends on the experience of a person performing the
measurement.
The EDA company offers measurements with the innovative method, using a
compact and mobile device for measuring forces in rods supporting the
structure of a power boiler – portable measuring device ED-SR-PMD-A01.
In order to improve the measurement accuracy, a pressure force control module (3) built in the device is used, which is attached between the surfaces (1) and (2), as
shown in the photo below. The device enables the automatic determination of the moment when the nut is being loosened.
⦁ Despite various boiler designs in power units and the resulting large variety of rod dimensions (different diameters, distances from the nut to the end of the rod), the device ensures easy installation and linear operation characteristics.
⦁ The measurement range of the device is from 0 to 400 [kN].
⦁ The device and its accessories and tools enable the measurement and adjustment of rods with a thread from M39 to M150 as well as inch and other threads from an adequate size range.
⦁ The system is equipped with a mobile recorder, with the possibility of rapid data copying to an external drive.
⦁ The device is resistant to dust and operation at high temperatures, up to 60 [°C].
⦁ Smooth operation of the pump and valves is ensured by pressure and temperature sensors coupled with the control system.
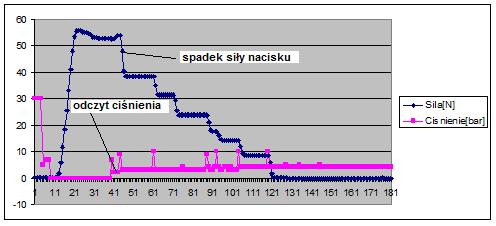
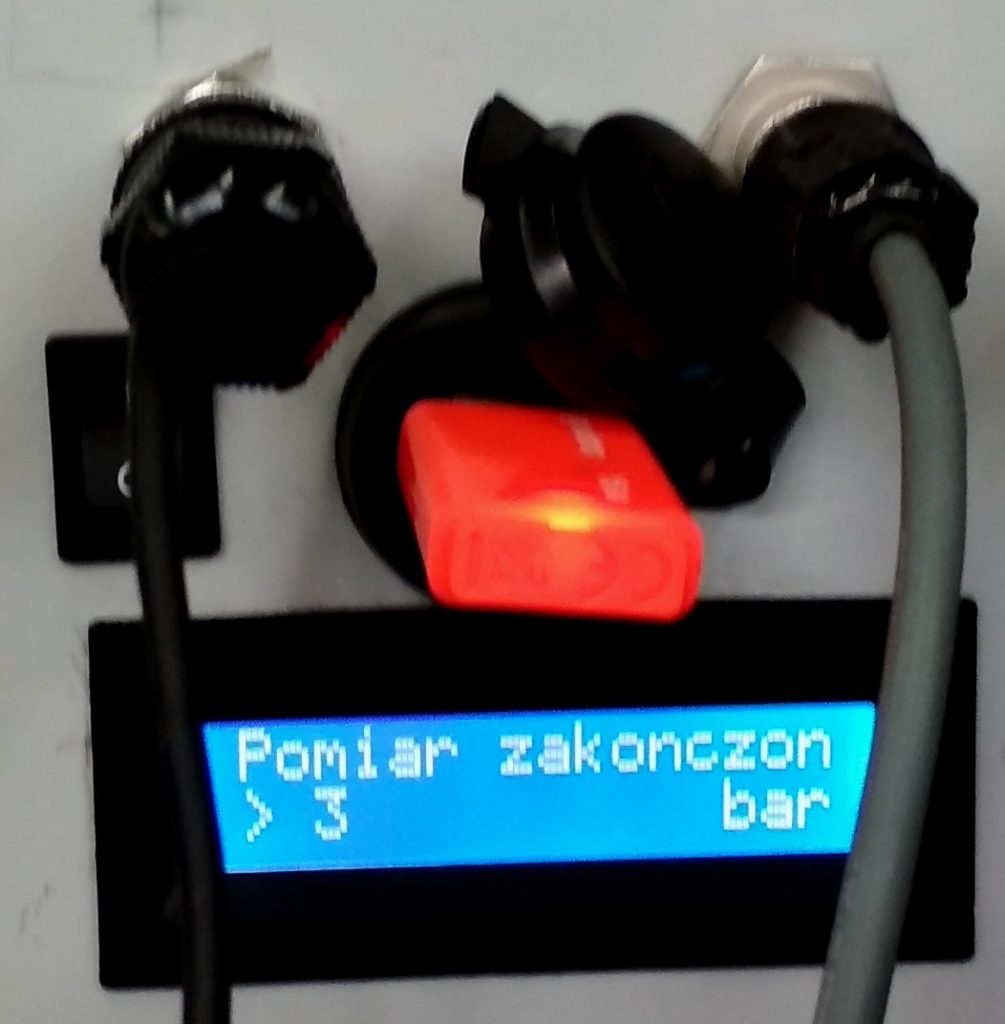
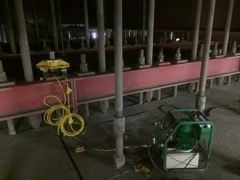
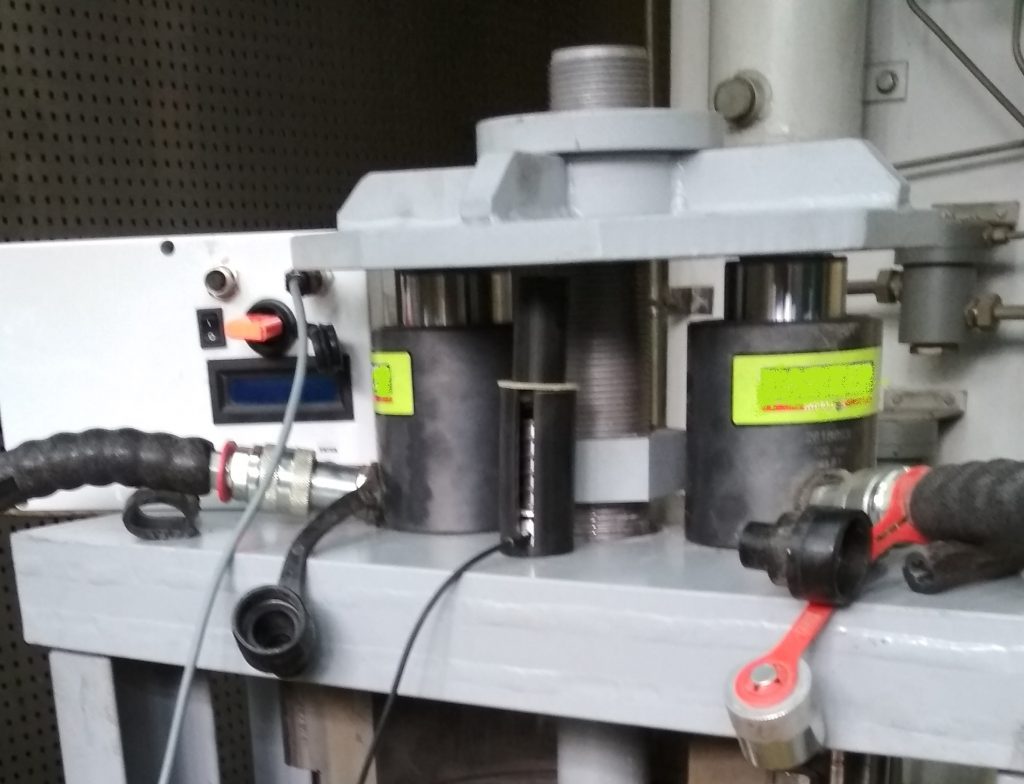
